Using a blind rivet nut to fix the bowden tube once for all
Blind rivets nuts give you a nut where you cannot reach the other side of the support.
An M6 blind rivet is also very appropriate to hold PTFE bowden tubes: the thread is long, and it is less bulky than a standard M6 nut. It is extremely robust in the end. And it even dissipates heat much more than the stock white clip as mine is made out of brass.
How to screw a nut on the bowden without damaging it
How to screw the nut without screwing the bowden tube ;-)
In order to screw the nut, I first sand the surface of the tube for a better grip. Then I insert a 3.8mm nail into the tube, so I can maintain the bowden with pliers without pinching it. I screw the nut with hand, or gently with another pair of pliers.
Adding a terminal nut to the hot end side
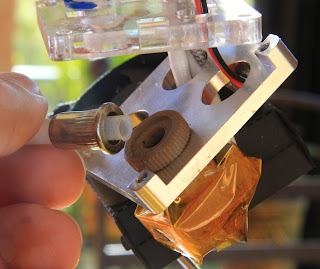
By chance, the base of this rivet perfectly fits the PEEK shoulder. There are other sizes, some of them really have a small base diameter, better check before buying (in case it matters).
Moreover, the rivet shoulder thickness makes it protrude a bit out of the PEEK.
I then inserted the bowden and nut from the bottom and tightened the 4 main long screws of the head assembly so that the nut stayed flat on the PEEK.
And more importantly, tightening more forces the bowden bevel to act as a sleeved seal on the brass top within the PEEK.
The final setup: there really is no way the bowden tube can escape upwards, now !
If ever I get a leak between the rivet and the PEEK, I will probably add a bit of automotive gold silicon joint (the blue one seems up to its temperature limit and get a bit viscous).